LEARN MORE ABOUT US
Different Types of Industrial Furnaces and Their Applications
Vasan Enterprises offers steel construction solutions to different industries like Manufacturing, Construction, Offshore, Marine, Oil & Gas, Railways, and Food & Beverages. Our range of products and services includes:
Vasan Enterprises is one of the industry’s leading industrial furnace manufacturers offers all types of aluminum melting furnaces. For any query contact us.
Vasan Enterprises is an industry-leading furnace manufacturer with access to a secure global supply chain, providing unique thermal processing solutions for a range of industries worldwide. With a catalog of tried-and-tested furnace designs and a suite of customization options, Vasan Enterprises is a cut above other furnace suppliers in meeting and exceeding client expectations. We also Provide
To know about Our Company
What is Industrial Furnace?
A furnace is a direct-fired device used to provide heat for industrial processes that require heat in excess of 400° C. Any industrial application that relies on heat to create a reaction or heat materials for production uses an industrial furnace. Of the many types of equipment and machines used for production and processing, furnaces are the most reliable.
Advantage & Specification of Industrial Furnace
Advantage
- High Energy Efficiency
- Affordability
- High Indoor Air Quality
- Fast Heat
Specification
Important specifications to consider when searching for industrial furnaces include:
- Process temperature
- Height
- Width or tube outer diameter
- Length of the chamber or tube
- Pressure range
The process temperature is the maximum temperature at which the unit may operate and still maintain rated performances. The height refers to the internal height dimension of the unit. The width refers to the internal width dimension of the unit, or for tube industrial furnaces, the outer diameter of the tube.
Types of Industrial Furnace
- Ashing Furnaces
- Calcination Furnaces
- Tempering Furnaces
- Annealing Furnaces
- Tensile Testing Furnaces
- Rotary Tube Furnaces
Ashing Furnaces
- Ashing furnaces are used to determine the amount of ash that forms after a sample is burned. Typical materials used as samples in ashing furnaces are petroleum products, lubricating oils, and coal.
- This process is often used to determine any contaminants in the sample, which are sometimes only present if ash is produced.
Calcination Furnaces
- Calcination furnaces are generally used to prepare raw materials for raw processing or to recover the base material following other processes.
- Calcination is a heat treatment process where samples including minerals or ceramic powders are heated below the melting point to induce phase transition, thermal decomposition, or to remove a volatile fraction.
Tempering Furnaces
- Tempering furnaces are often used after iron-based alloys have been subjected to hardening or quenching, which can cause excess hardness, stress, and brittleness.
- Tempering is the process of heating steel to a specific temperature and then cooling it in still air.
Annealing Furnaces
- Annealing is a heat treatment process that is used to soften a sample for improved cold working, and machinability, and to enhance mechanical and electrical properties.
- Annealing furnaces work by heating up material and maintaining the temperature before cooling at a suitable rate.
Tensile Testing Furnaces
Tensile testing furnaces are used to measure the ultimate tensile strength, yield strength, strain-hardening, and a range of other properties of a material.
Rotary Tube Furnaces
Rotary tube furnaces are circular furnaces that rotate during heat treatment and are often used for continuous materials processing as they can apply heat in multiple thermal control zones.
How do you build an aluminum melting furnace?
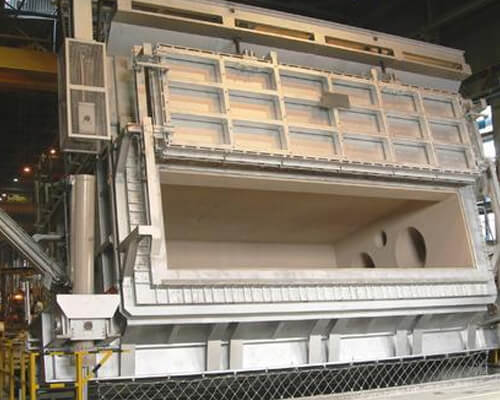
Aluminium Melting Furnace Manufacturers in Chennai
- Aluminum chips are challenging to melt due to their tendency to float on the surface of the molten aluminum when added to most furnaces.
- An aluminum chip melting system utilizing a traditional coreless induction furnace can help overcome this with its inherent stirring. The stirring helps submerge and break up clumps of aluminum chips, allowing them to be melted more efficiently than in a furnace with little or no stirring.
Advantages of Using Induction Melting Technology for Melting Furnace
- Operational flexibility
- Increased Efficiency
- Better or Cleaner Metal Quality
- Better Work Environment
Key Takeaways: Melt Aluminum Furnace
- Aluminum is an abundant and versatile metal that is easily recycled.
- The melting point of aluminum is low enough that it can be melted with a hand-held torch. However, the project goes more quickly using a furnace or kiln.
- Recycled aluminum can be used to make sculptures, containers, and jewelry.
ONE STOP
SOLUTIONS FOR ALL
YOUR INDUSTRIAL FURNACE NEEDS
GET A FREE QUOTE!
Equipment Division
Steel Fabrication & Erection Services
Shutdown & Maintenance Works
Our Recent Blogs
Find us on maps
Working Hours
Monday | 9:30am–6:30pm |
Tuesday | 9:30am–6:30pm |
Wednesday | 9:30am–6:30pm |
Thursday | 9:30am–6:30pm |
Friday | 9:30am–6:30pm |
Saturday | 9:30am–6:30pm |
Sunday | 9:30am–6:30pm |
Get Your FREE Quote Today!
We are available 24/7 by email or telephone. Call or Text!